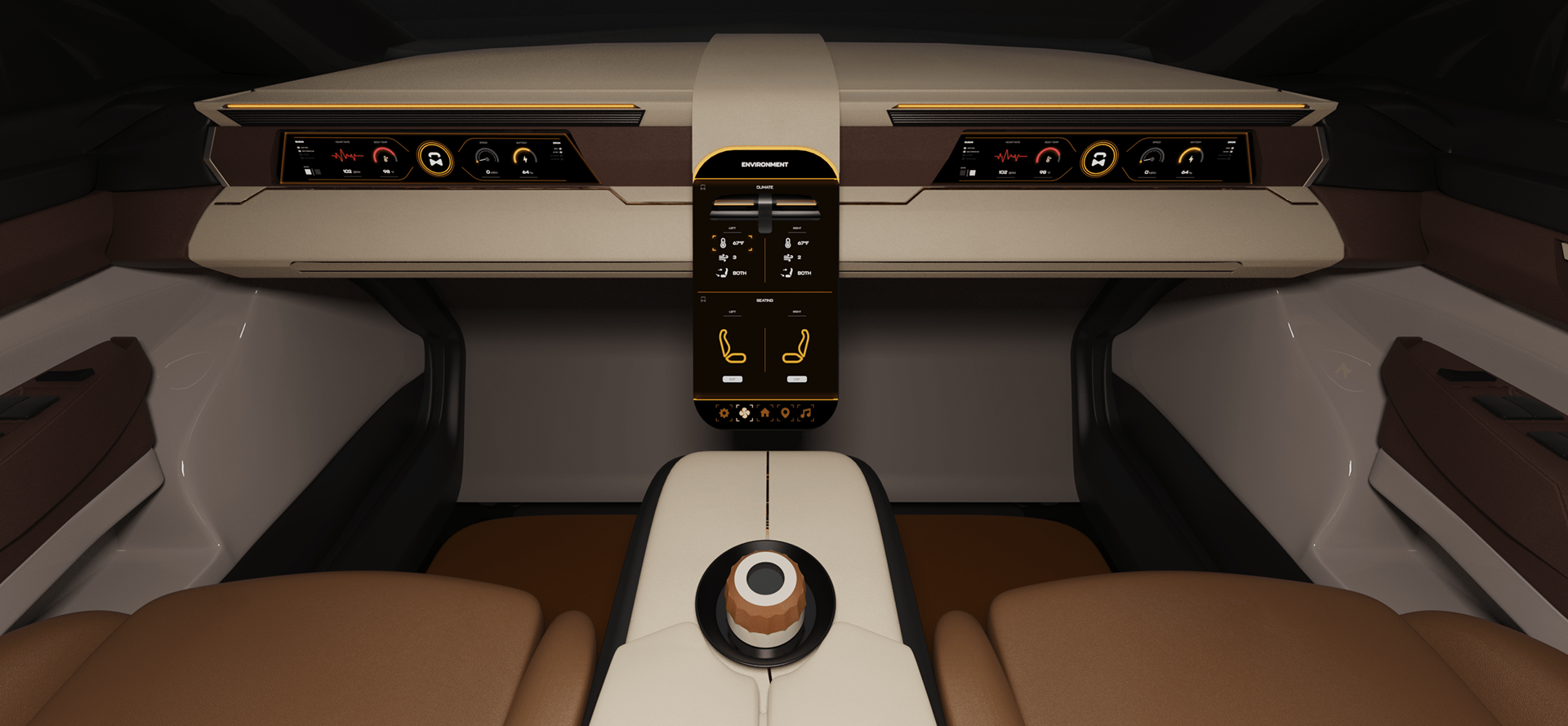
The internal knob design is currently undergoing the patent application process with General Motors and cannot be shown. The following information provides a general overview of this project. For product specifications, please reach out to me directly.
PROGRAMMABLE HAPTIC KNOB FOR L5 AUTONOMOUS VEHICLES.
design brief: Developing a patented, single point of control and interaction for a GM vehicle's interior system in a level-5 autonomous setting that provides haptic, ergonomic feedback based on user task and input.
team: J. Clements, J. Hsu, K. Seo, Z. Mock, K. Yang, T. Zhang
role: Project Manager + Product Designer
Working with in the Mechanical Engineering-Industrial Design Capstone Studio, our team worked in the GM-GT Human-Machine-Interaction Lab to develop a patent-ready knob design for future General Motors vehicles.
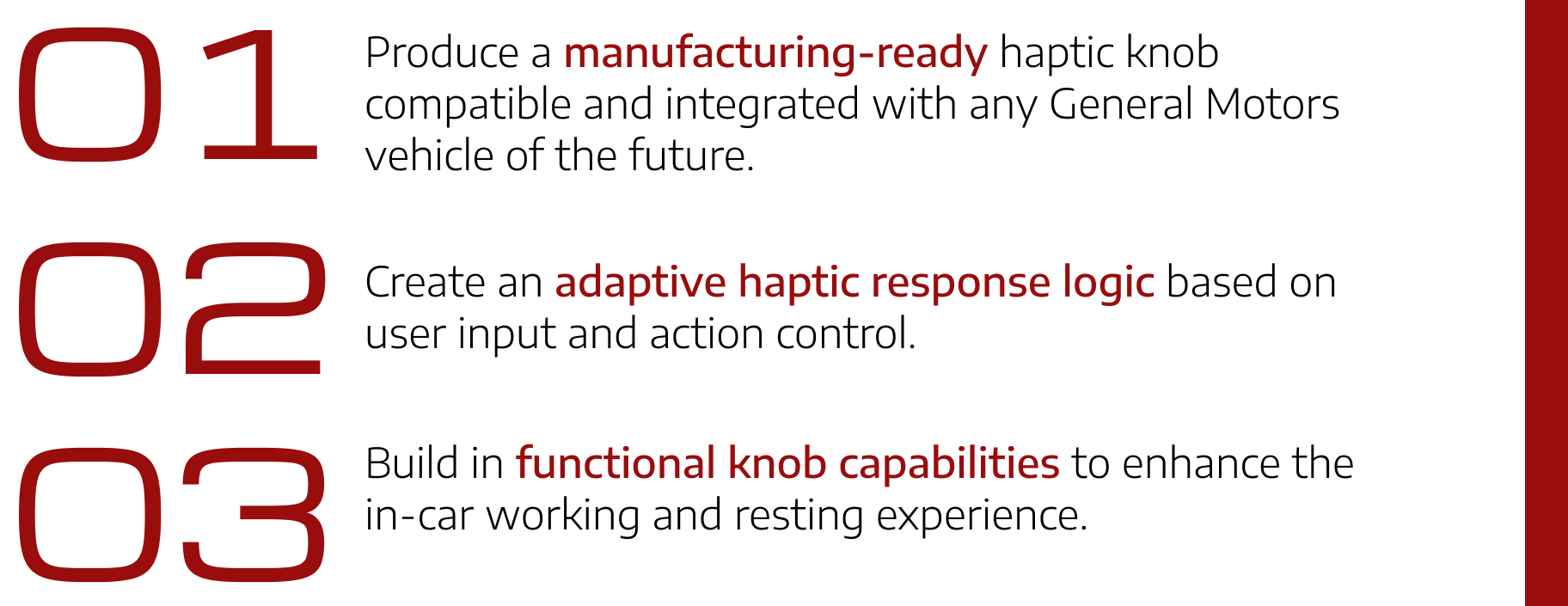
PATENTING APPLICATION.
Our project worked as a continuation of previous work developing the interior design of an autonomous vehicle, who had suggested a central knob control and requested our team to design it and prepare it for patent submission with General Motors. Our team's goals were created with this in mind.
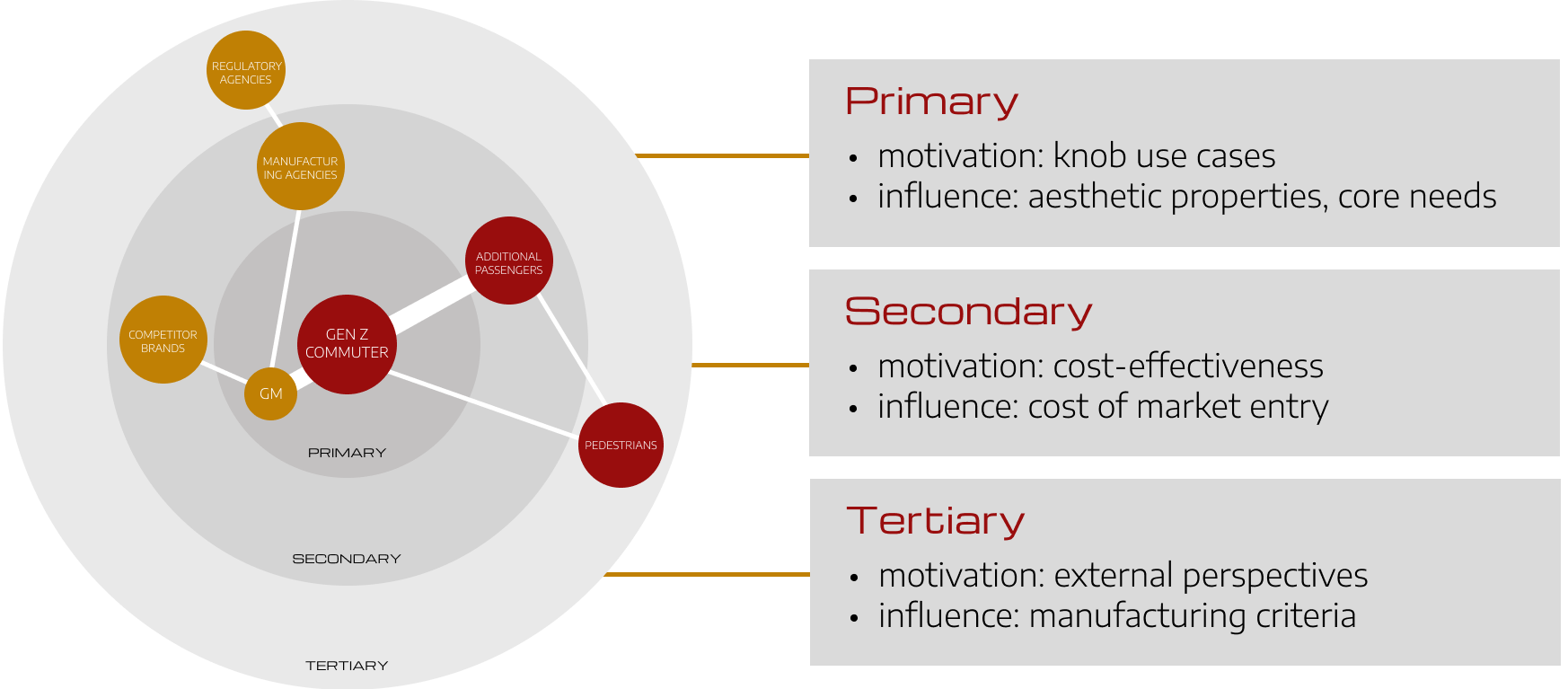
STAKEHOLDERS.
As GM is a large company with many customers, our team focused in on the Gen-Z Commuter as the target user demographic for a haptic knob within a level-5 autonomous vehicle, with target years of implementation starting in year 2035.
THE COMMUTING EXPERIENCE.
In an L5 vehicle, the "driver" no longer exists. Instead, the experience becomes one of commuting, where users are able to accomplish other tasks as they travel from one place to another. To define what the Gen-Z Commuter wanted to do in this setting, we surveyed this demographic and used their opinions to guide our design decisions regarding the actions we wanted to test the knob with.
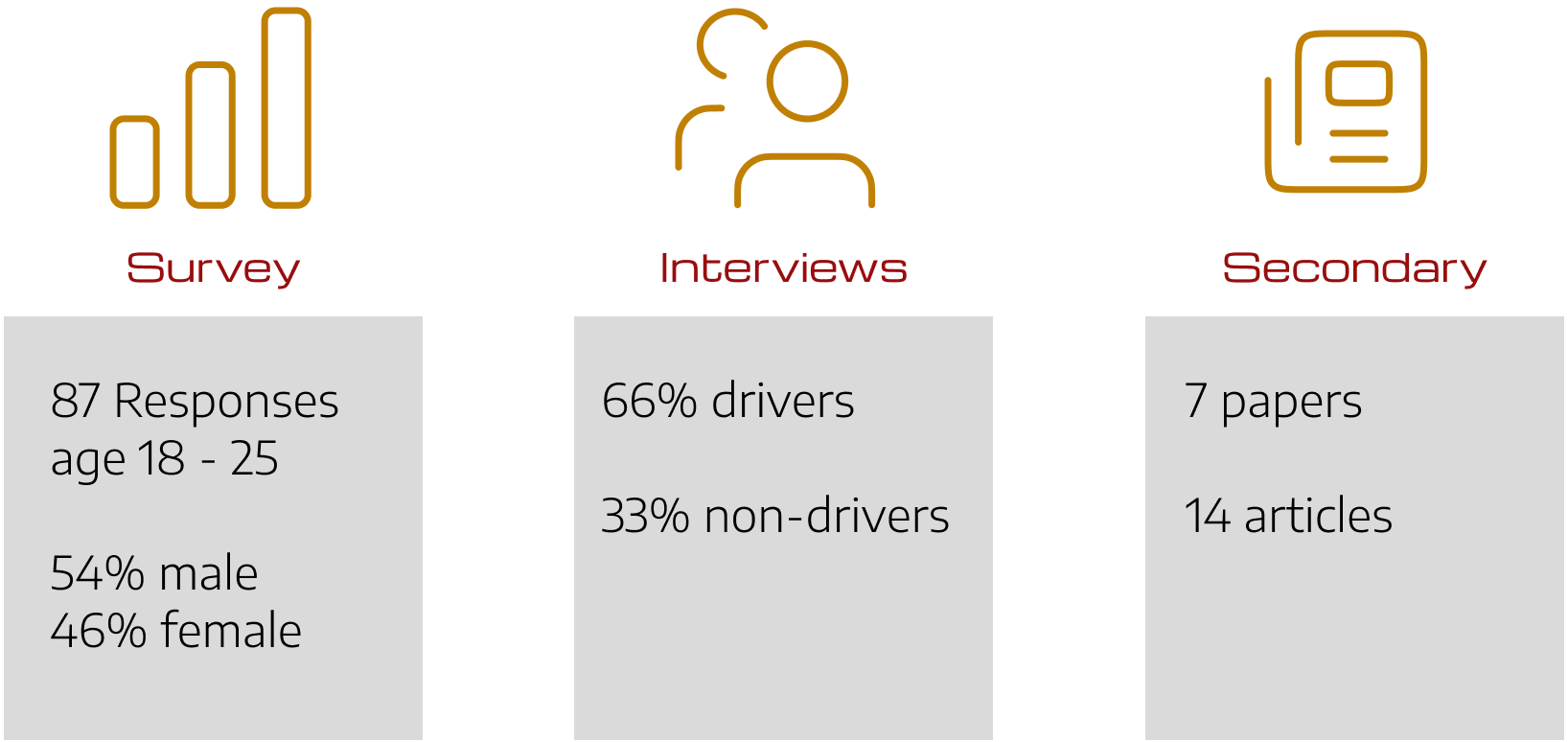
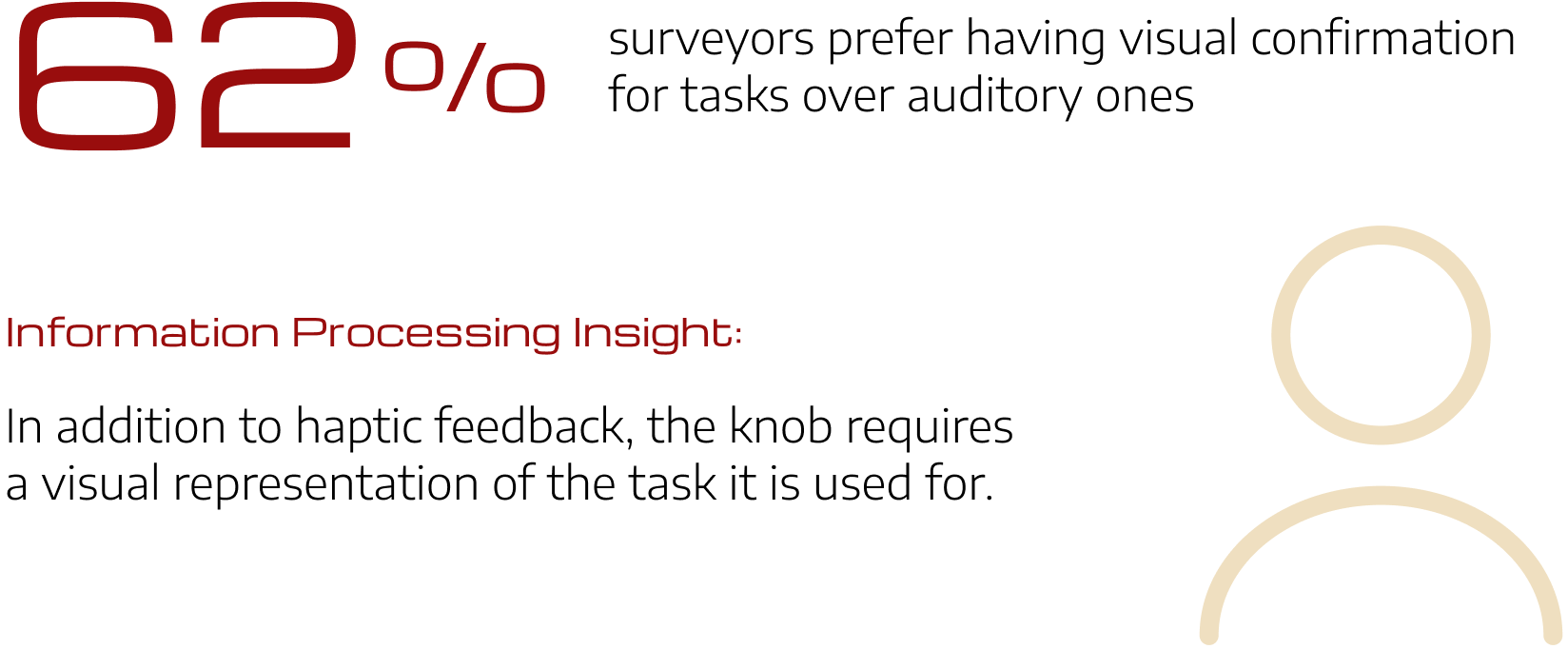
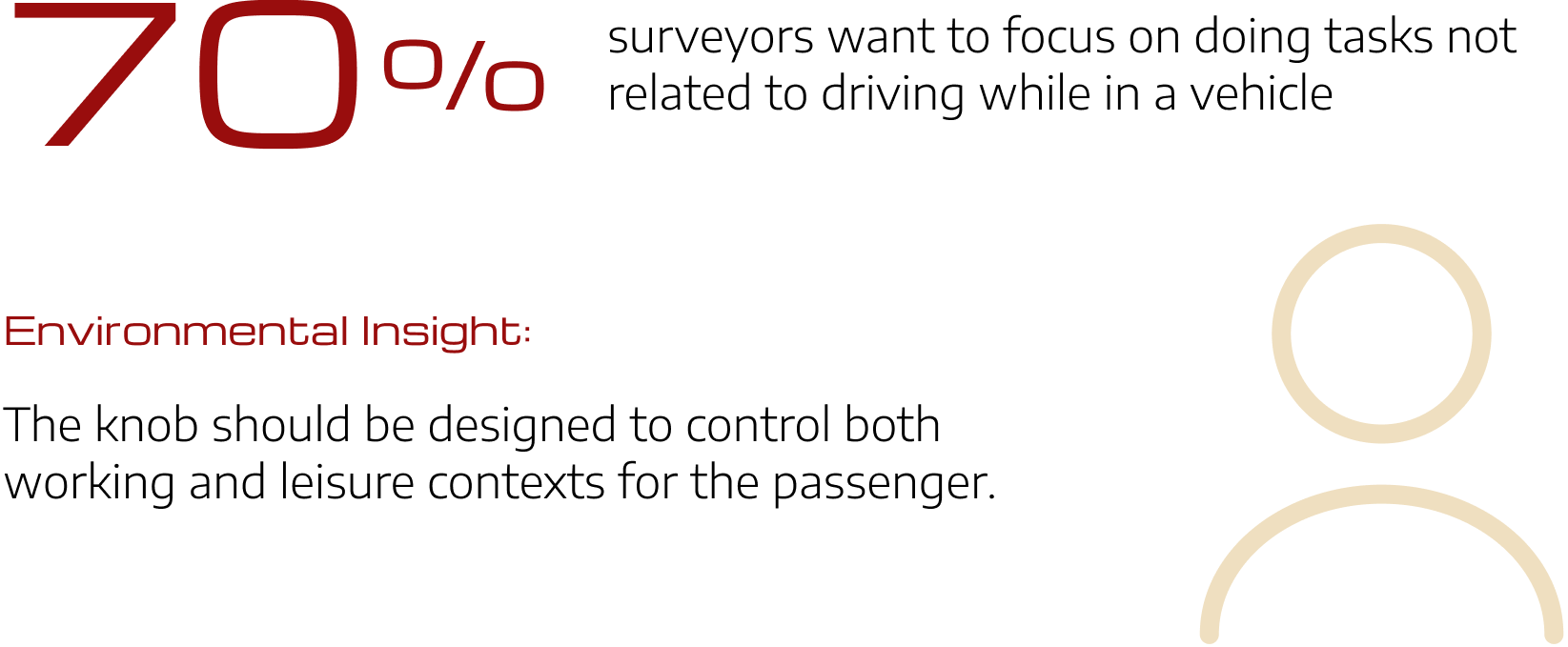
TASK DISTINCTION.
Based on our findings, we defined three tasks for the user to test our knob's haptic feedback and functions with: two tasks would represent the distinction between a Work Mode Task and a Relaxation Mode Task, and a third, general action to act as a baseline for knob function mechanics. This improved on existing research by directly applying user needs to the knob for a more tangible use case.
WORK MODE.
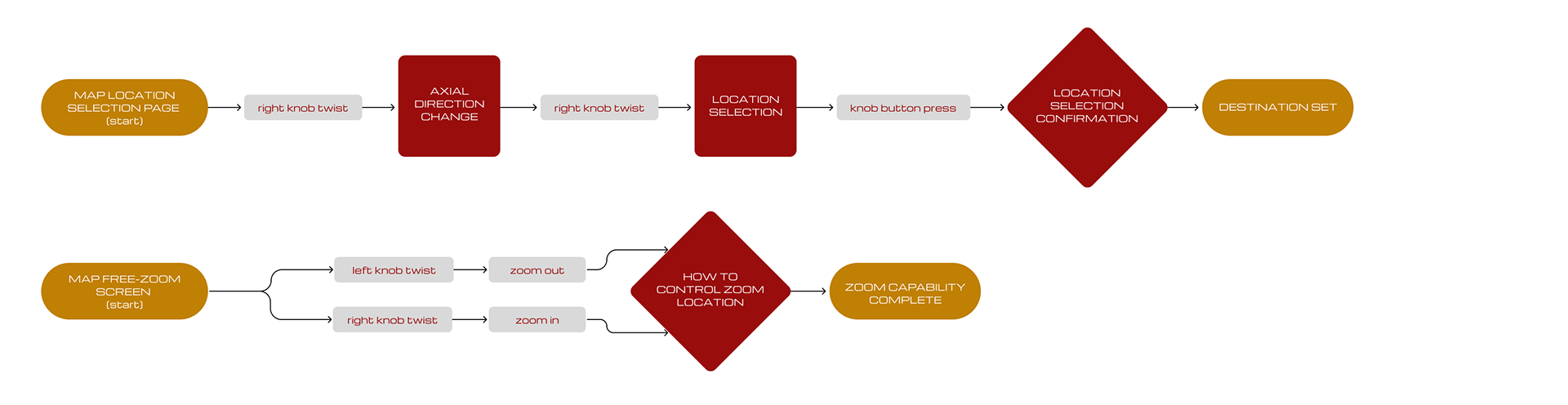
RELAXATION MODE.
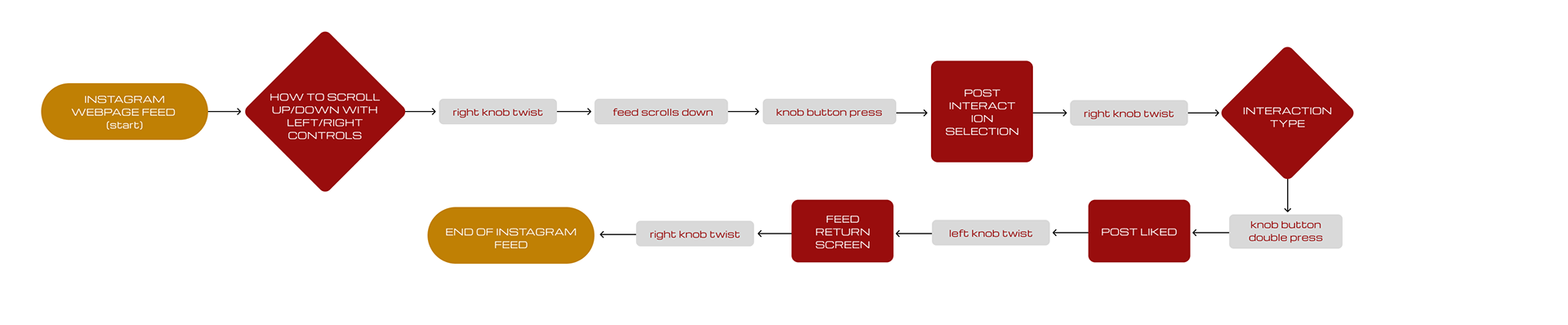
BASELINE ACTIVITY.
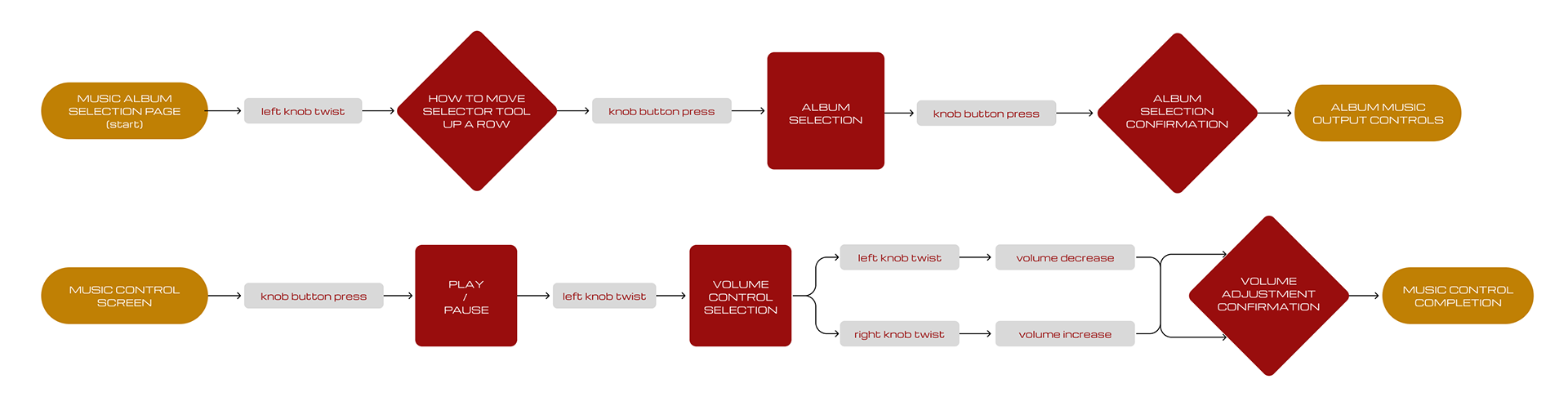
FORM DEVELOPMENT.
Alongside internal mechanical development for knob electronics, I conducted four separate rounds of user testing for the external knob shell design. Initial calculations were based on NASA Anthropometric Measurements and Humanscale Data Sets for optimal hand grip dimensions, then tested with users through an iterative design process to modify details such as texture patterns and taper angles.
TEXTURE SPECIFICATION.
User testing indicated a strong preference for an extruded texture pattern around the knob alongside a smaller texture pattern on it for optimal interaction. To maximize feedback, I 3D-printed multiple 2D texture patterns for users to feel, with the most popular designs added to a physical 3D knob prototype for contextual use. Directly based on their feedback, the final outer shell specifications were solidified.
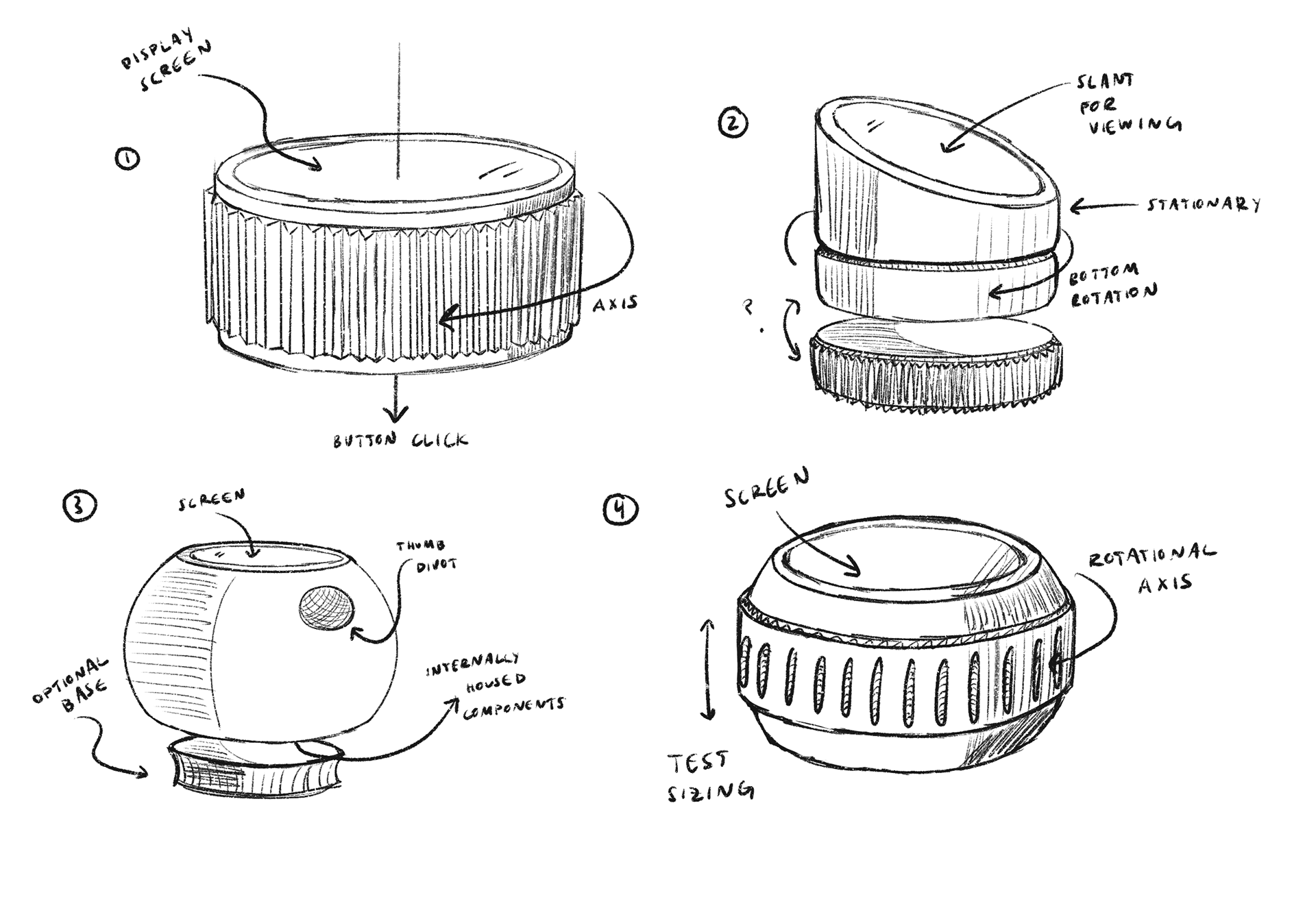
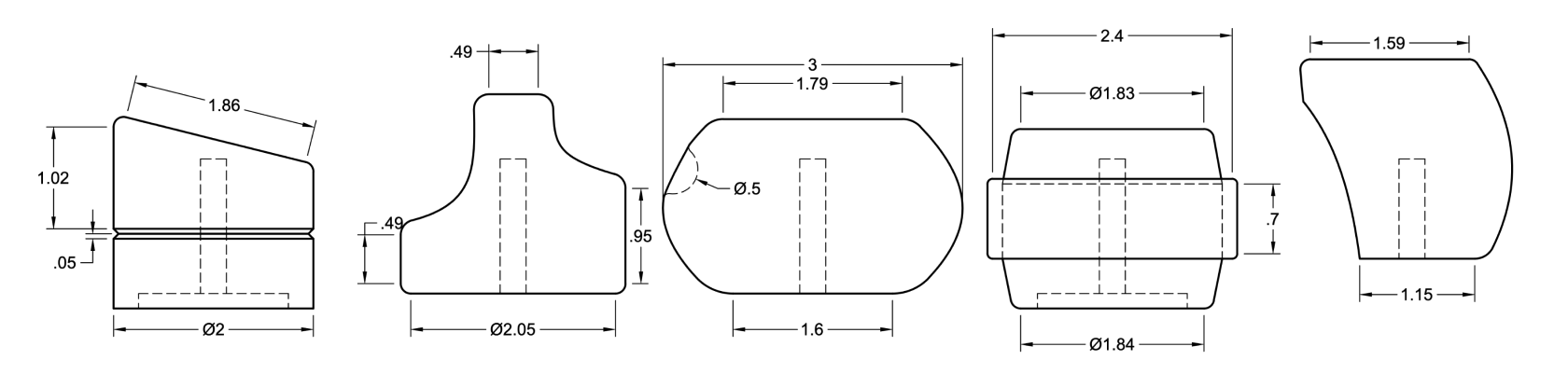
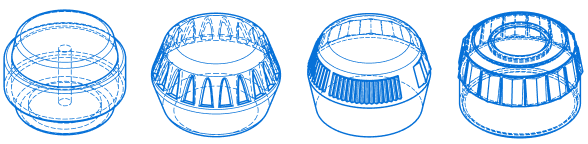

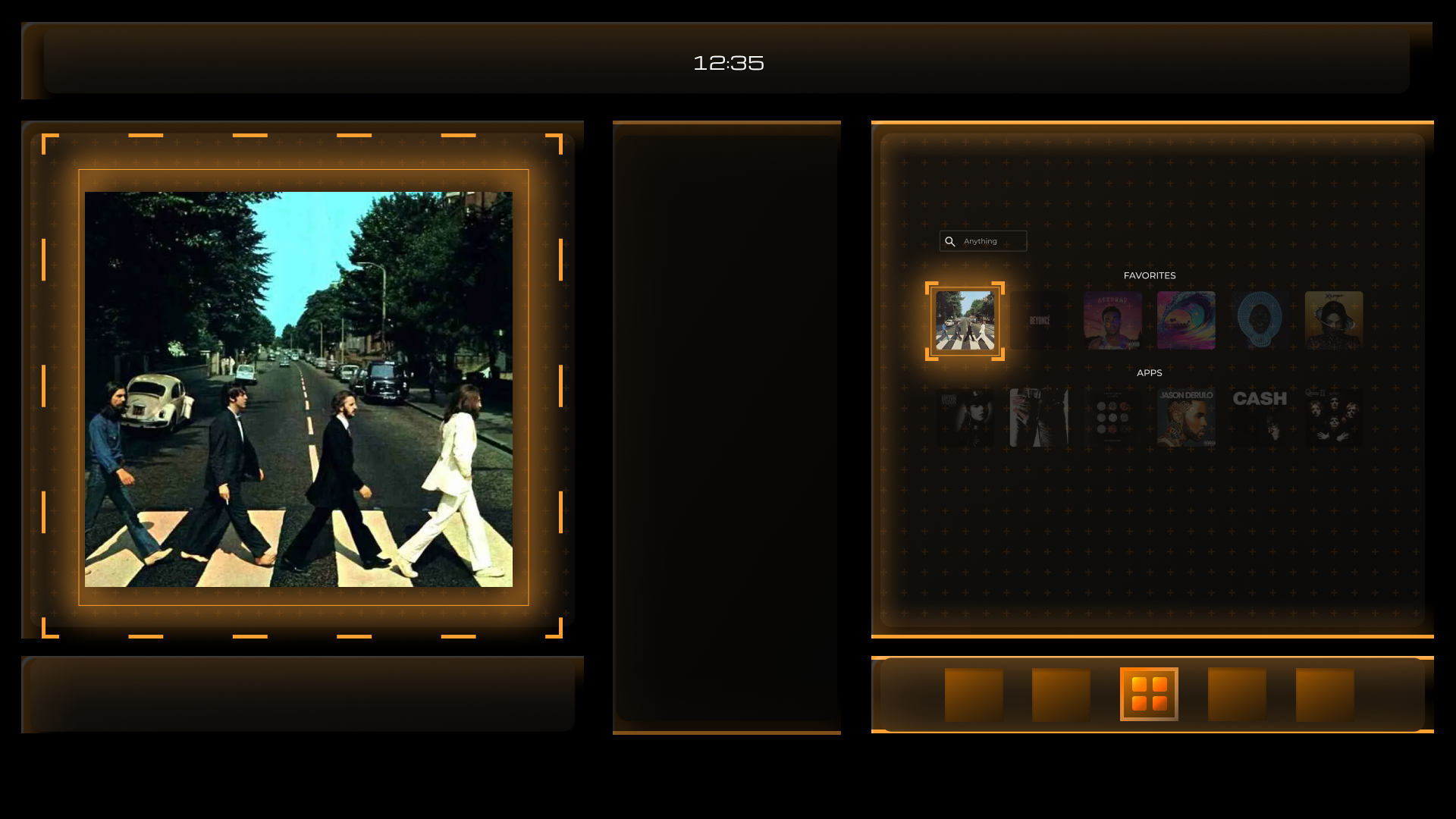
USER FLOWS.
To simulate the tasks in an interactive haptic environment, I created three Figma interfaces that each reflected the intended design of an L5 autonomous vehicle interior. Our team mapped each haptic knob output combination to a key-bind to connect the physical prototypes from form exploration with the digital interface for users to test, rather than go through the difficult process of manually creating a new human-machine interaction language. Biometric data for each activity provided the results to determine our design success by calculating stress and cognitive load levels.
As an example of our user testing setup, I recreated the Instagram page to utilize our knob's new scrolling and bi-directional movements with the ability to select, like, comment, and send posts within a Figma prototype.

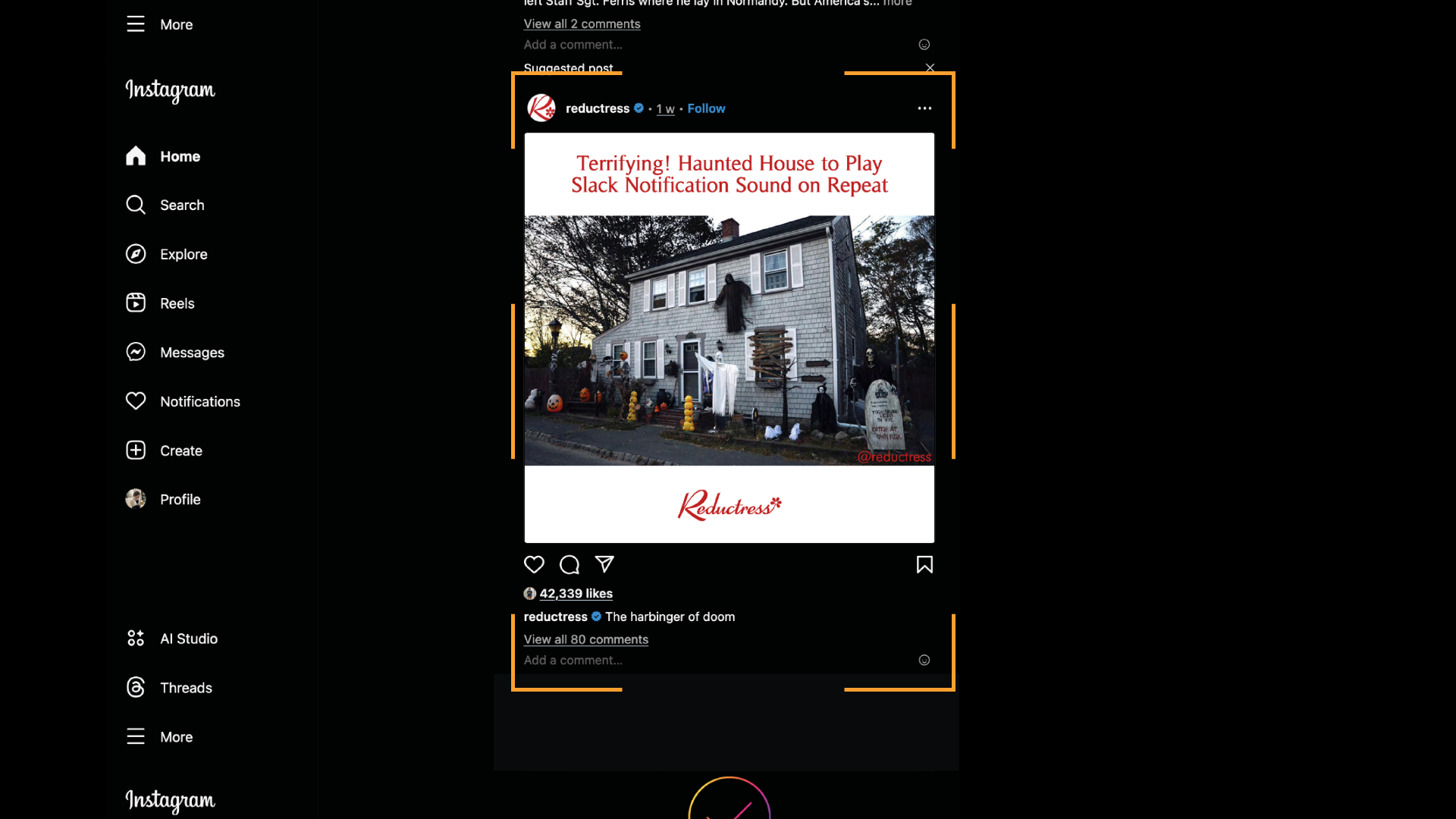
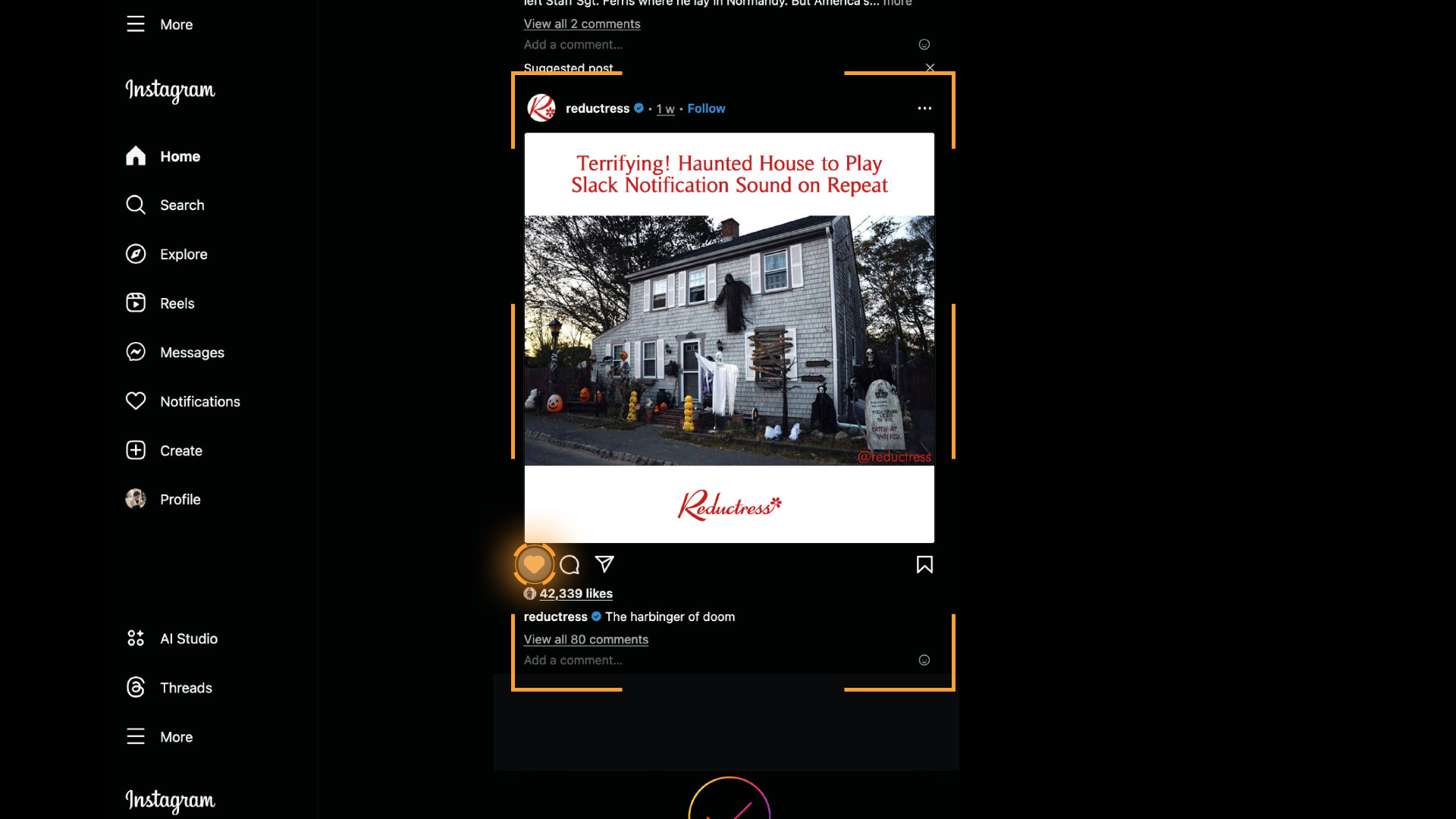
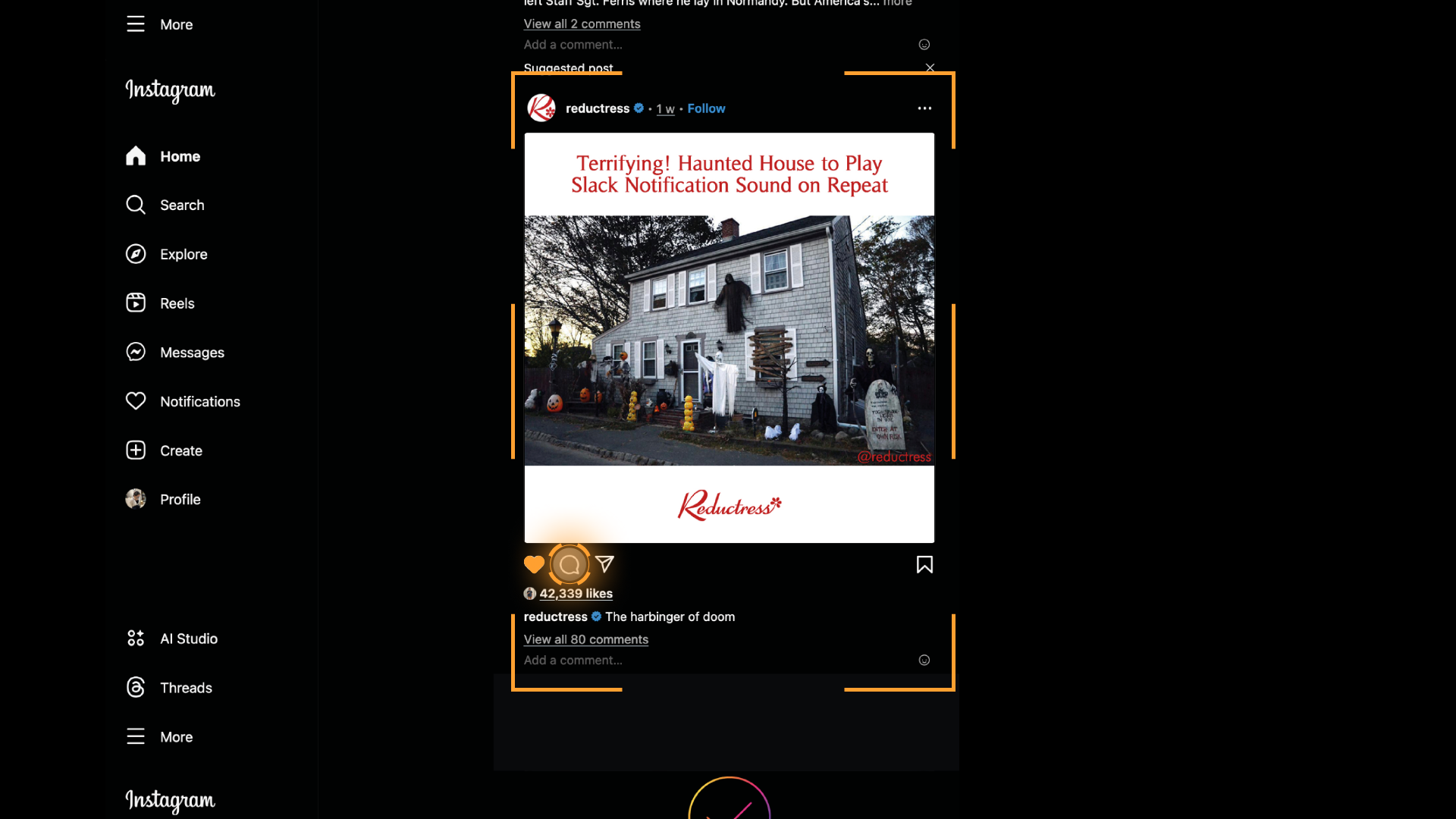
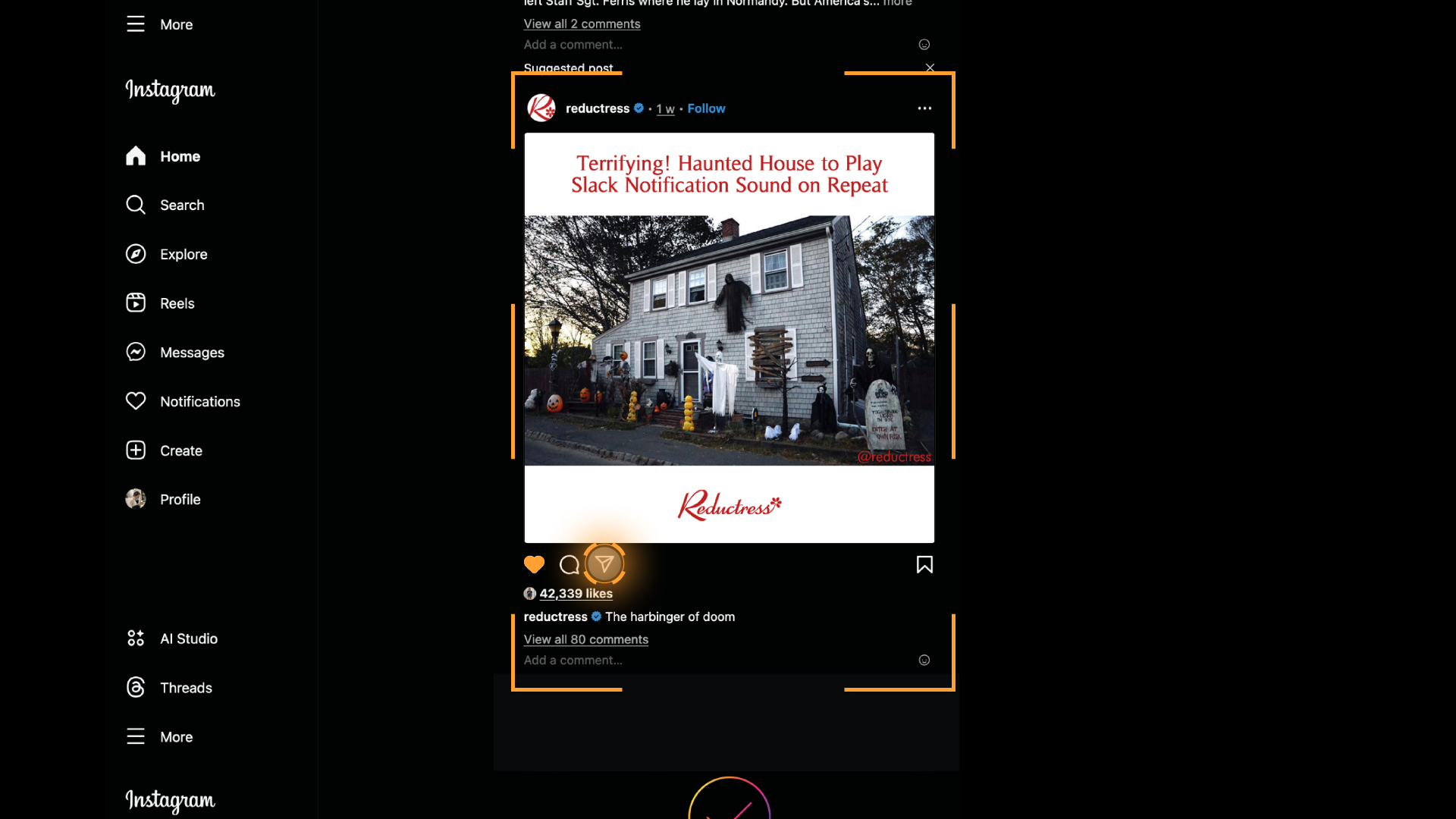
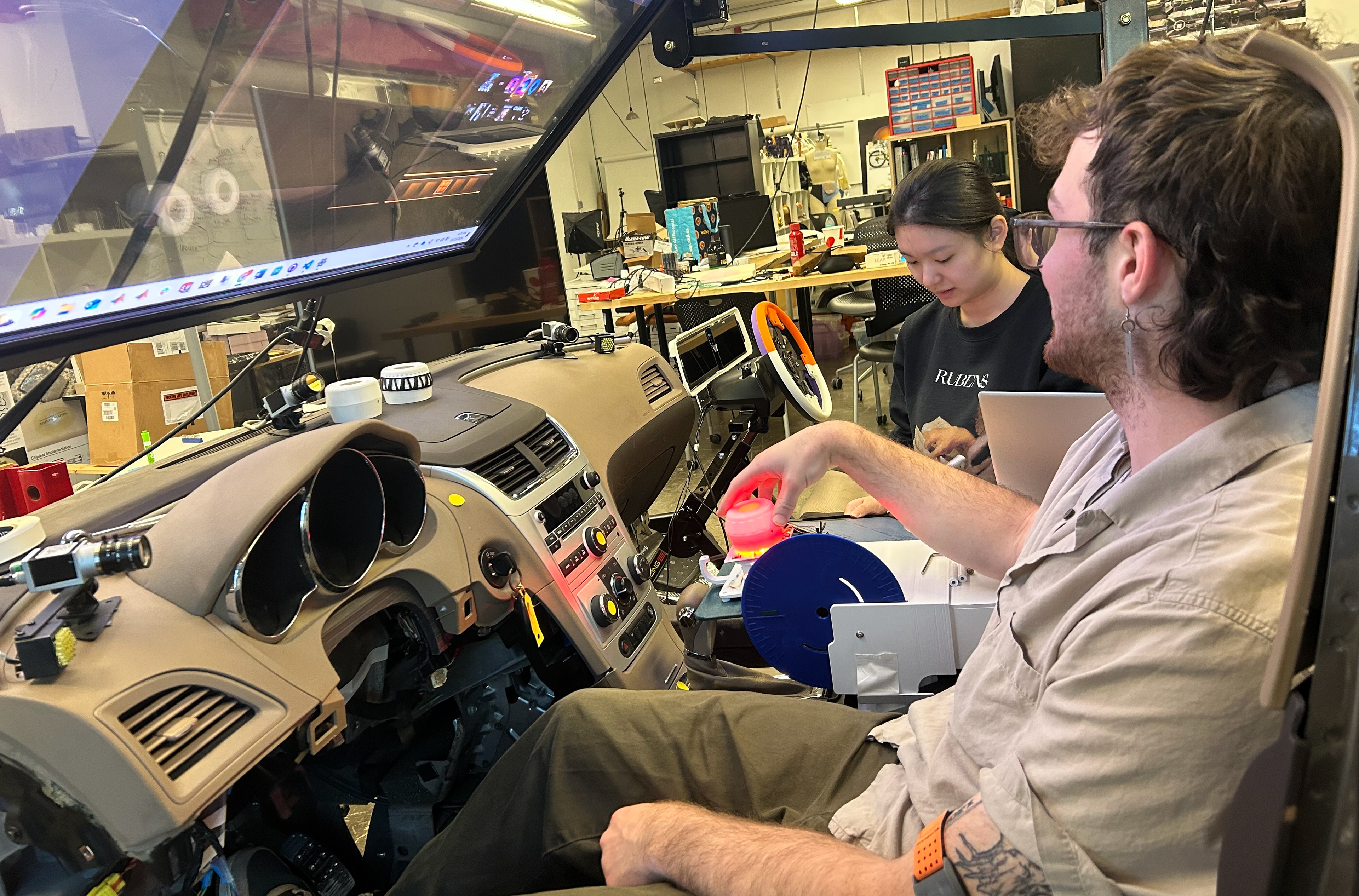
TESTING ENVIRONMENT.
The setup for user testing used an O.L.E.D. dash display and the interior front seating of a modified Chevy Malibu with its steering wheel removed to simulate an accurate autonomous driving setting. Users would sit in the simulated driver's seat and interact with the knob to control the main display to test ergonomics and haptic intuitiveness.
DESIGN FOR MANUFACTURING.
Both the outer knob shell and its internal components have been designed to fit industry manufacturing standards for mass-production injection molding techniques. The plastic finishes, surfacing texture, and colour choices have been defined using global standards such as Mold-Tech and Pantone values. This ensures a customizable design that each application can reproduce and modify based on individual needs.
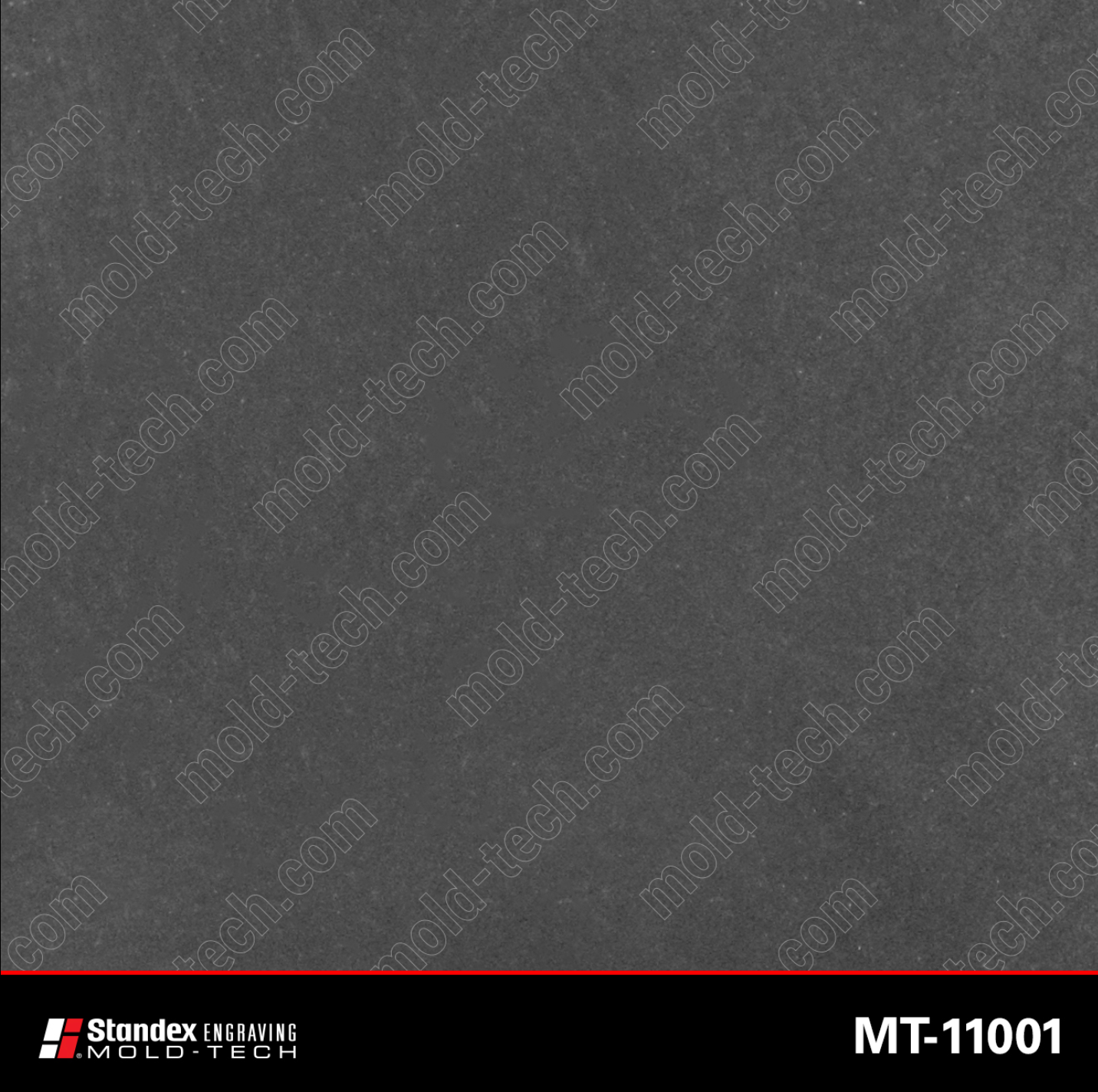

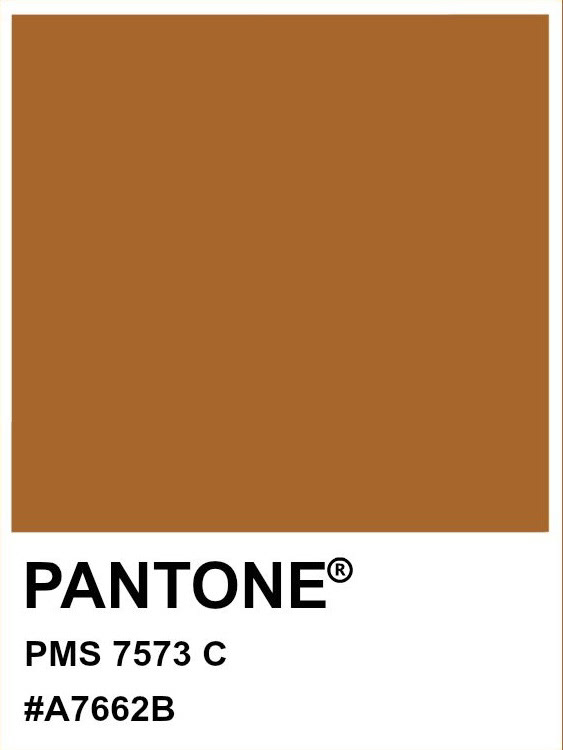
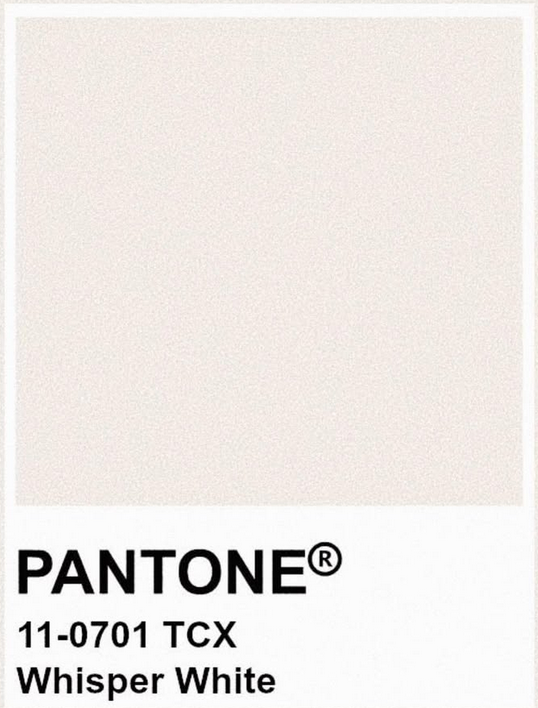
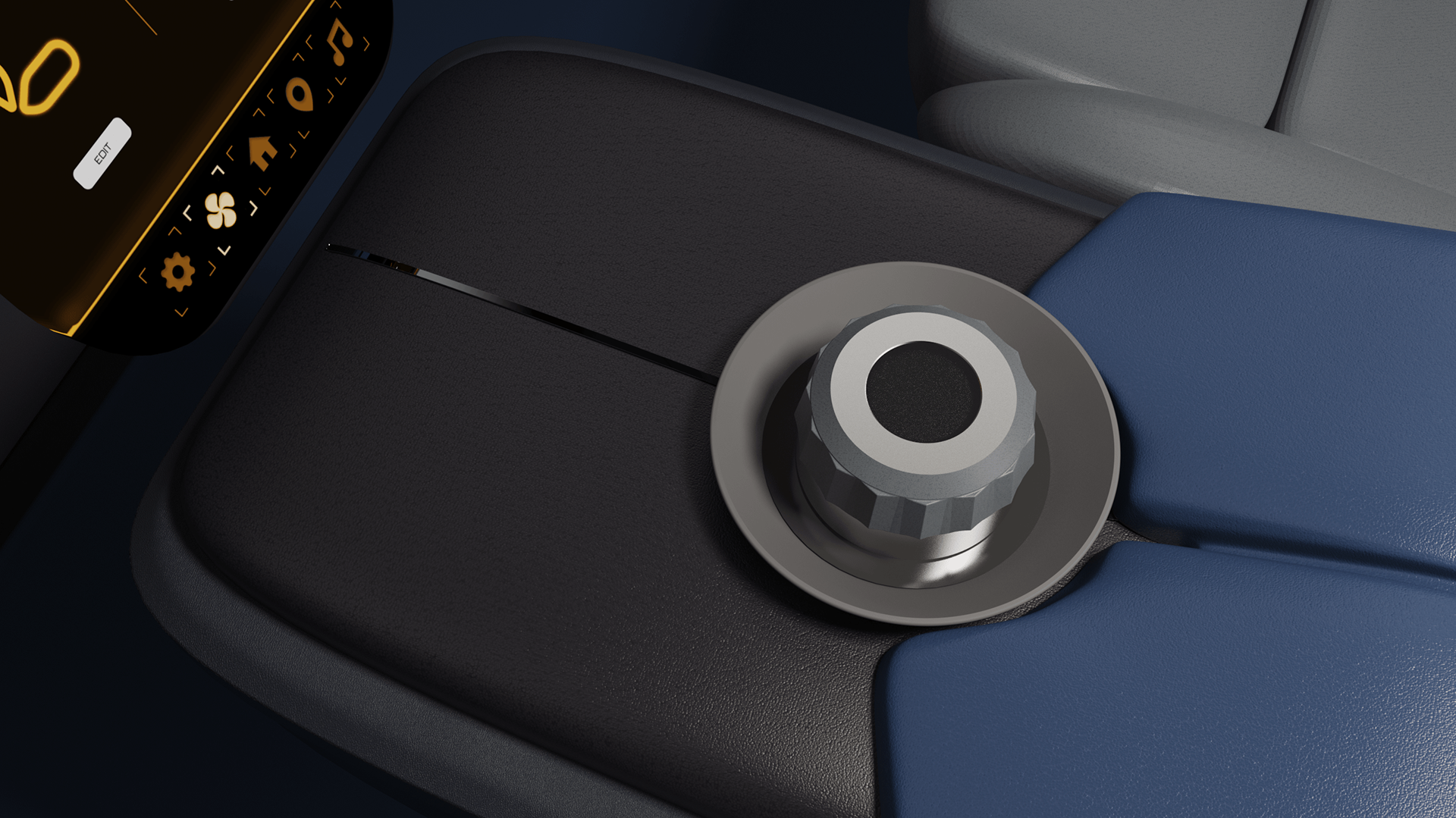
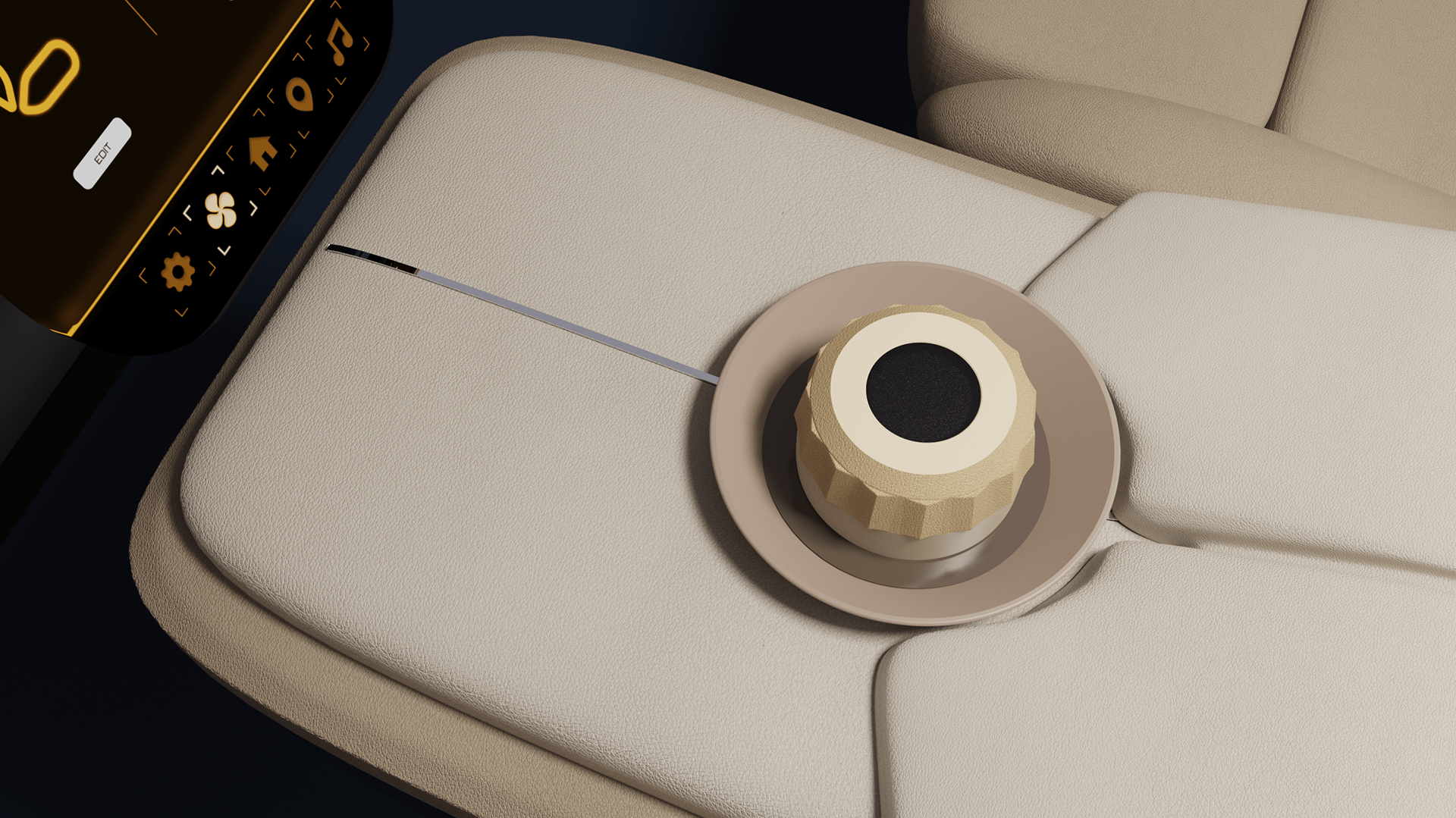
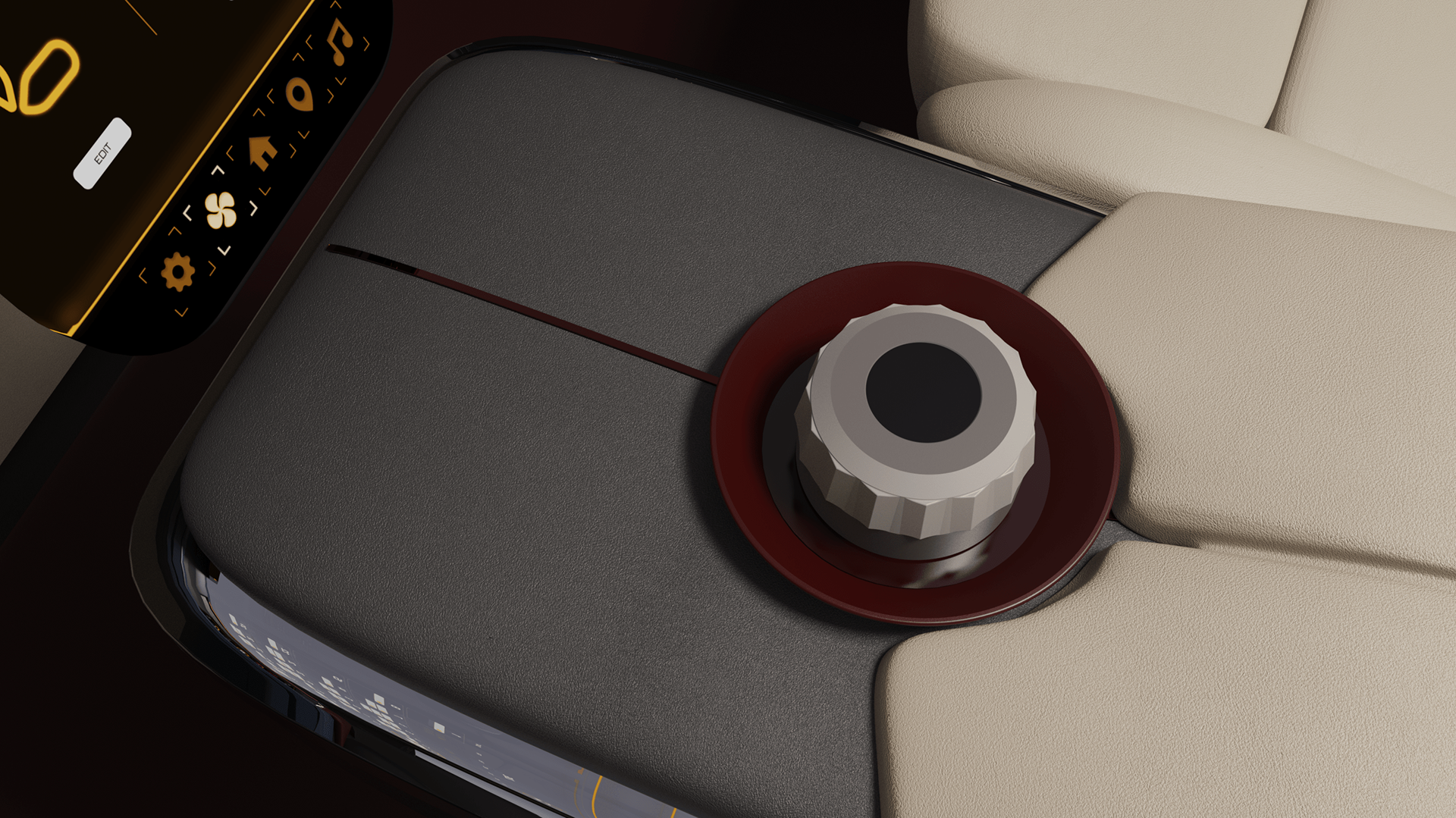
DESIGN FOR AUTOMOTIVE ENVIRONMENTS.
A difficulty in previous development prior to our team was focusing on creating a durable design that was made to specifically withstand an automotive environment. Our team focused on selecting waterproof outer materials and added interior sealants such as silicone o-rings and glass covers to protect the electronic components from potential dust or liquid. Stress tests were conducted on each assembly part to ensure absolute functionality for up to 70 pounds of applied force to simulate possible passengers from knocking into the knob.
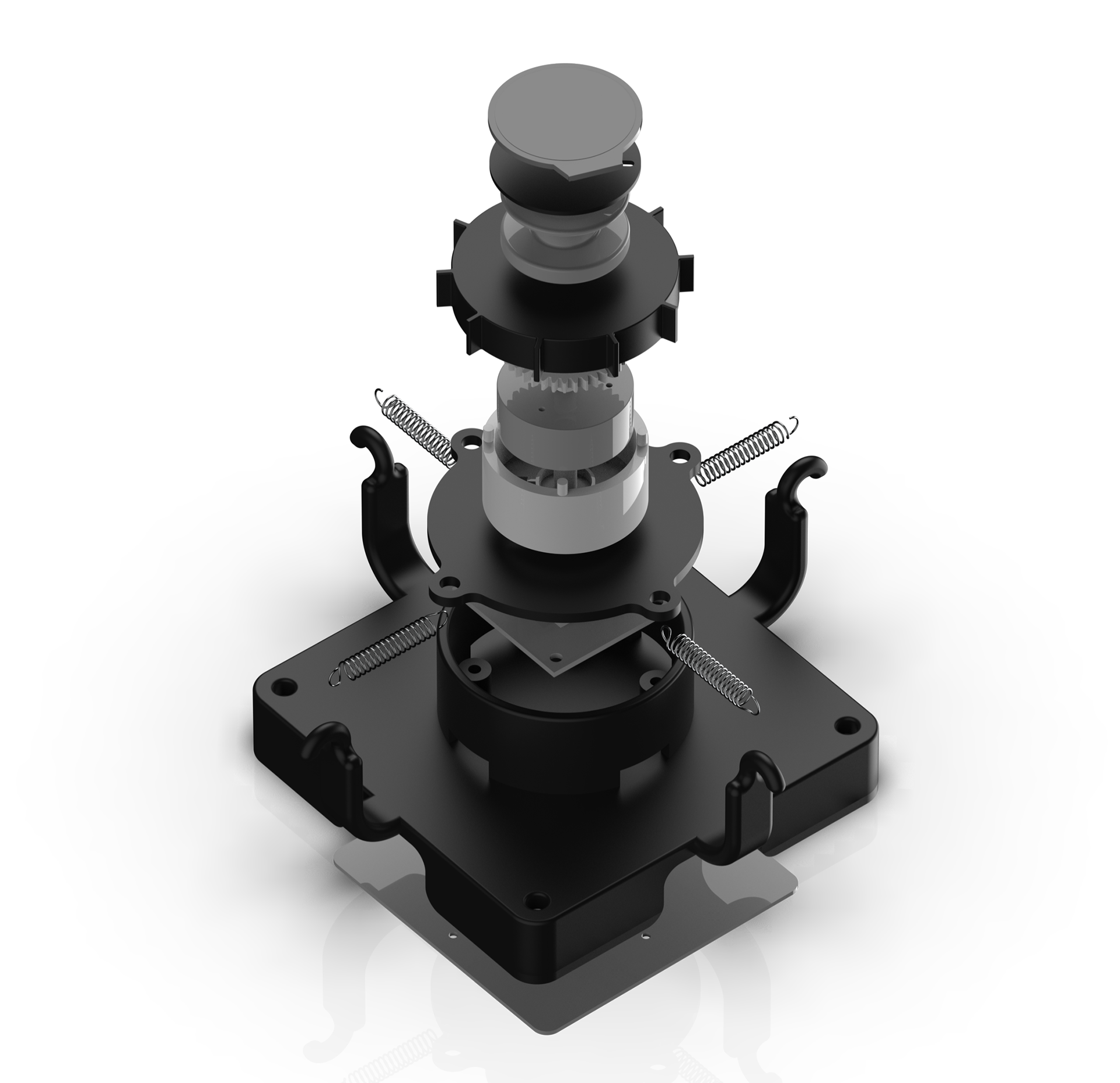
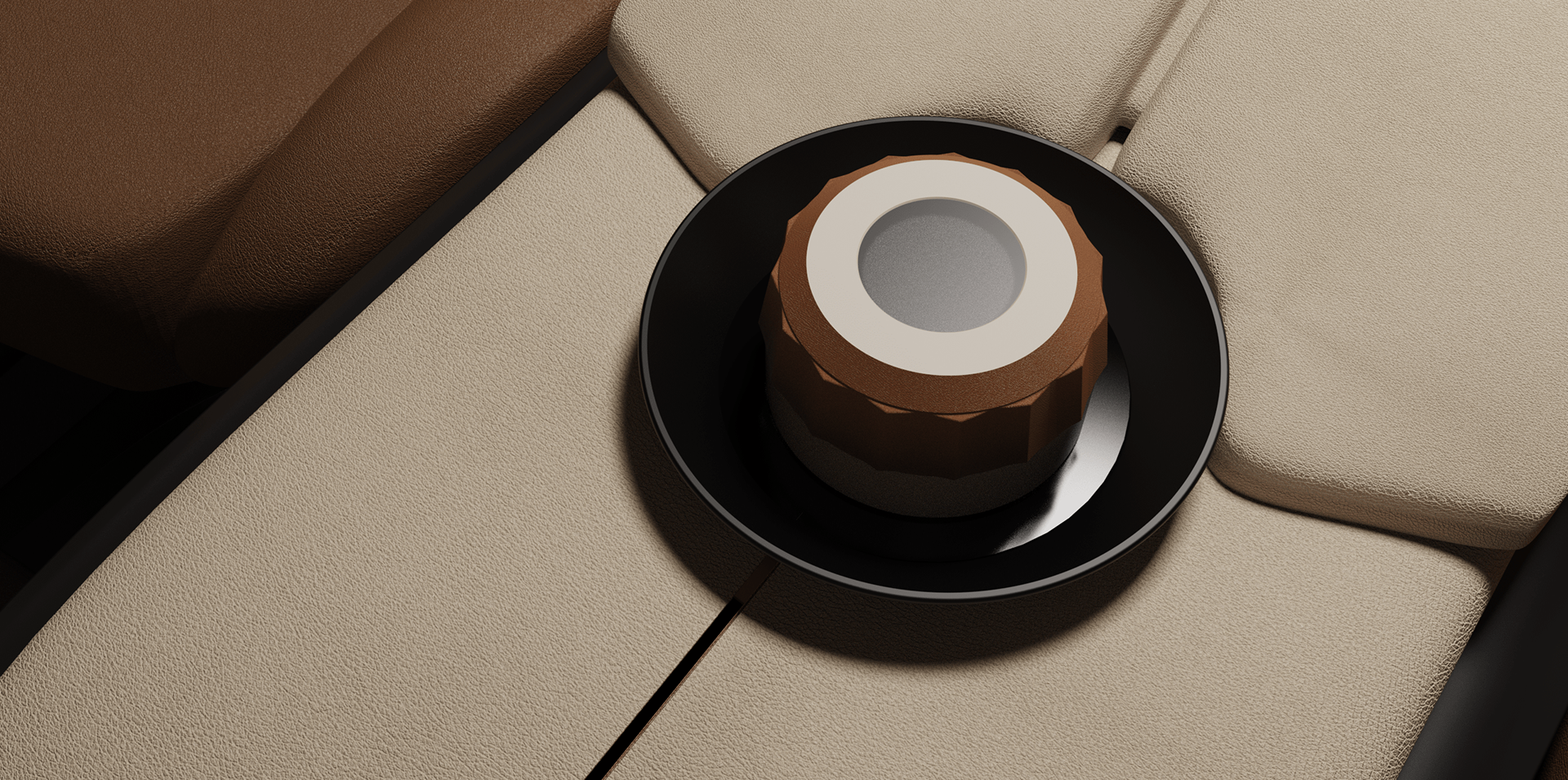